Merck reduces incidents by building a culture of safety awareness
When a global healthcare organisation that’s been around for 125 years wants to drive a proactive culture of safety across its 52 global manufacturing sites, it takes more than setting up seminars and putting up posters. It takes shifting the mindset of each and every employee.
Merck has always put safety front and centre among numerous competing corporate priorities. However, its safety record wasn’t where the company wanted it to be. Leadership saw areas for improvement and set a new goal of Target Zero which means “even one incident is one too many,” according to Sanat Chattopadhyay, President of the Merck Manufacturing Division (MMD) and Executive Vice President of Merck.
The company’s leadership team recognised that a simple training program, based on the same old safety training procedures and policies, was not going to be enough to engage employees in a meaningful way.
After all, Merck & Co., Inc. (known as MSD outside of the US and Canada) is no stranger to impacting the lives of millions through its innovative approach to medicines and vaccines, so it only made sense to apply the same outside-the-box philosophy to the safety of its employees.
The primary goal of MMD was to build a strong culture of safety throughout its network of 52 global manufacturing sites to ensure that safety best practices were not only top of mind, but ingrained in the attitudes and behaviours of all employees. The leadership team knew if they could make this happen, everything else — reduction in incidents and injuries, informed and engaged employees, increased business results — would follow.
They were right.
Creating consistency in culture
In early 2016, Eagle’s Flight, an industry leader in the development and delivery of practical training programs, helped MMD implement its program Safe by Choice™ (SbC). The program is aimed at boosting safety awareness and reducing incidents across the company’s manufacturing network of approximately 24,000 full- and part-time employees and partners. This program consisted of classroom sessions, additional training for people managers, and weekly SbC tools that were used throughout the year. Tools such as, print material, digital signage, and the Axonify solution which leveraged safety questions and reminders at each weekly group meeting — from the highest levels to the shop floor.
The Axonify platform starts with the business outcomes first. With a unique combination of microlearning, gamification, and adaptive learning — Axonify builds employee knowledge, sustains it over time, and provides knowledge-on-demand capabilities when employees need it most. This was crucial to rolling out the SbC program, since MMD needed a way to embed safety principles into the minds and behaviours of every individual, no matter their location, age, or skill level.
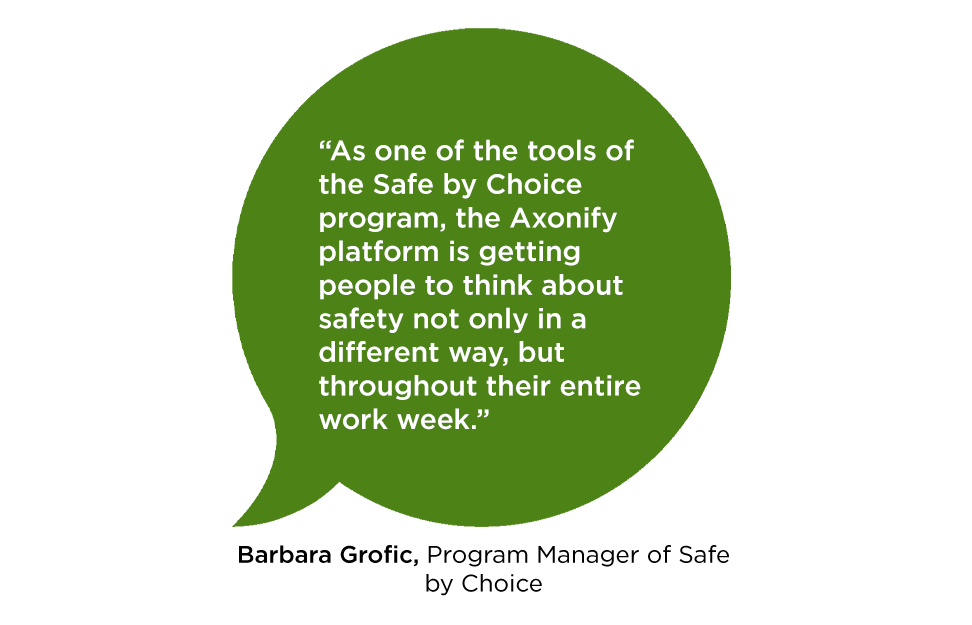
Of course, the company is no stranger to safety training. Many of the organization’s larger sites had very robust safety programs. In fact, some integrated sites with multiple divisions even had their own safety council that included representatives from the shop floor, all the way up to higher management. “The problem was the message wasn’t consistent across the divisions or the company,” says Barbara Grofic, Program Manager of Safe by Choice.
It’s the same situation many large organizations find themselves in today — with multiple sites and divisions spread out across the globe, all different in character. Some are small, some are large, some are unionized, and some have a great safety record, while others could use improvement. Across such large organizations, it makes sense for different sites to have different challenges around safety.
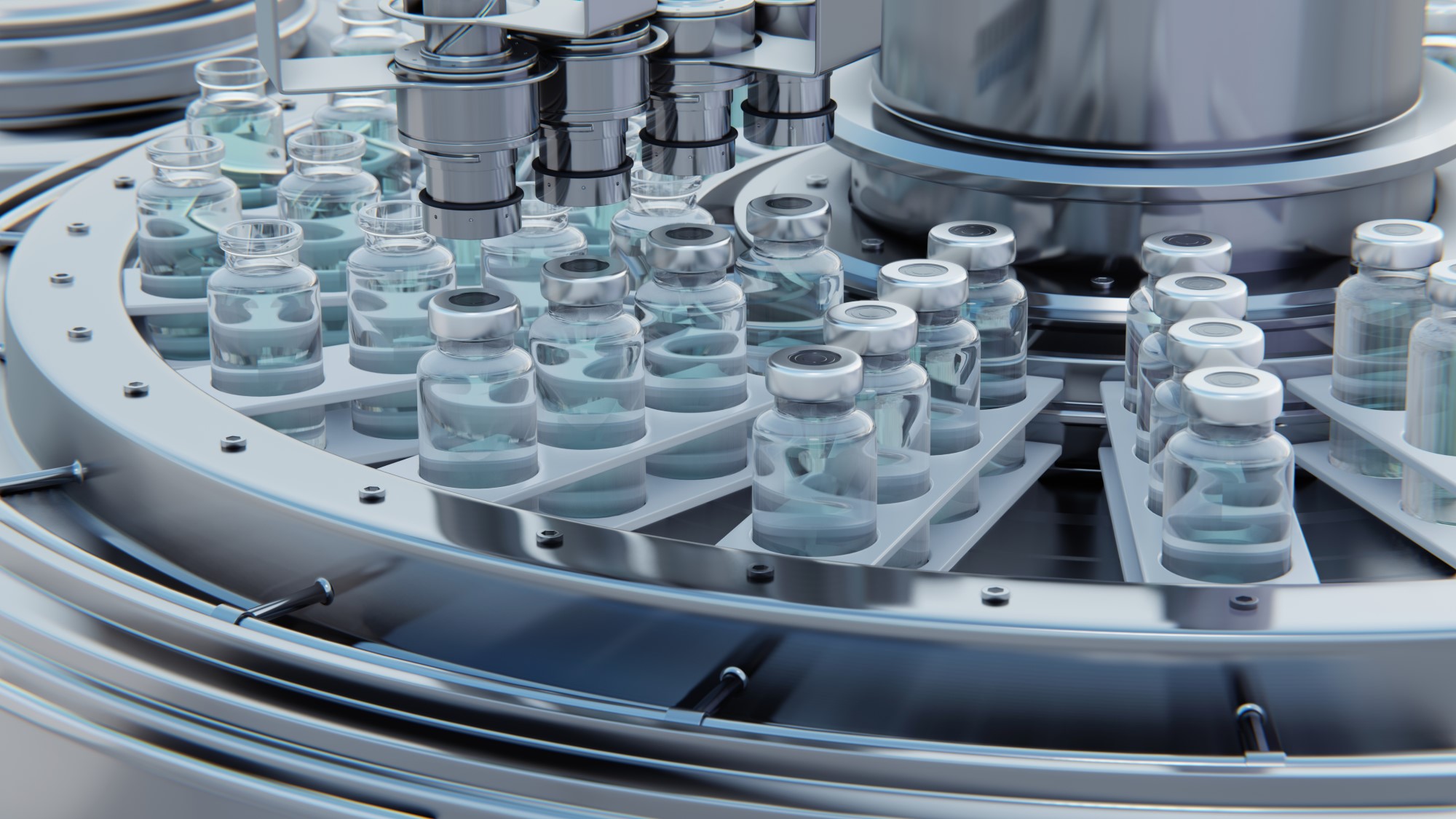
Don’t just mitigate risk — extinguish it
According to Grofic, MMD’s leadership team saw an opportunity that had the potential to make a “huge impact, with low risk.” The company knew it needed to build a consistent program, which started with building a collective culture around proactive safety. MMD President, Chattopadhyay says, “The only way we can ensure that we mitigate risk, or even extinguish risk, is when we have a very astute understanding of the why’s and how’s of every unit of operation.” This means communicating a consistent message across all locations, all generations, and in all relevant languages. After that, reinforcement ensures each individual embodies the same values in their day-to-day lives, on the job or at home.
To drive impactful change throughout a large organisation, it really has to start with a shift in mindset with each individual, at every level. “We have seen significant value with the Axonify platform. There’s been a lot of energy around it with people logging on more than once a week and challenging each other,” explains Grofic. “It’s a great way to not only reinforce safety principles and procedures, but create energy and excitement around our entire Safe by Choice program — from those on the shop floor who touch the products, up through the highest levels of plant management.”
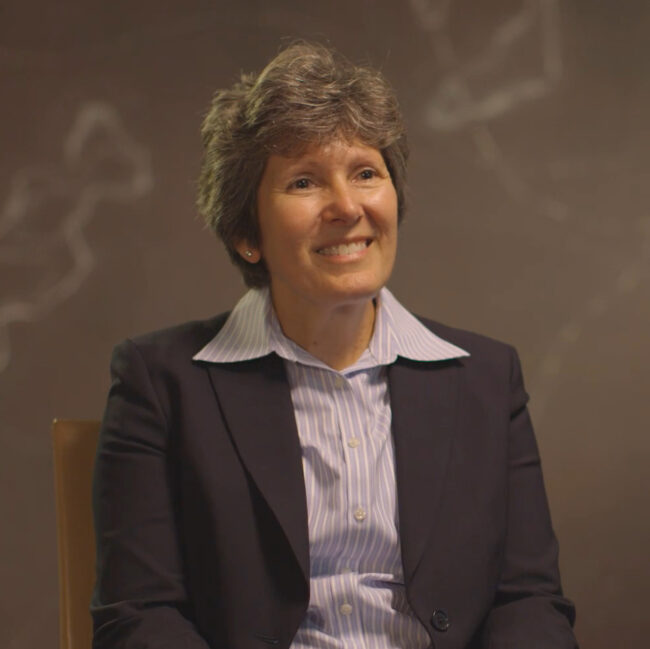
Sustainable safety in every language
Running through safety orientations as protocol for onboarding is not the most effective way to engage employees and instil safety behaviours that will stick. Companies need to get their people to start thinking about safety in a different way. In order to do that, consistency is key — and not just in the message they communicate, but in the cadence, frequency, and medium or channel they use to disseminate that message. Grofic explains, “As one of the tools of the Safe by Choice program, the Axonify platform is getting people to think about safety not only in a different way, but throughout their entire work week.”
In just a 12-month timeframe, adoption of the Safe by Choice program and the Axonify platform has skyrocketed. MMD has sustained more than 80% voluntary participation levels, on a monthly basis, in the US, Italy, China, Brazil, Spain, Japan, Singapore and many other countries. With such high participation rates from MMD’s employees, the leadership team plans to continue using the Axonify platform to keep its employees safe. “We had never done something like this with such a vast audience before, but leadership realises there’s a true benefit in keeping safety front and centre in the minds of our folks,” explains Grofic. “Instead of letting it be something that’s discussed on a quarterly or bi-annual basis. Our people are discussing it weekly.”
The Axonify platform also supports content in more than 10 languages, keeping MMD’s global safety message consistent across all manufacturing sites. In fact, MMD now boasts a “common language” of safety across all of its global manufacturing sites and has succeeded in embedding its safety practices into the company’s culture.
Results continue to tell the same story. Across 52 global sites, knowledge of safety topics is up, the recordable incident rate is down, and lost time injury frequency rate is down compared to 2013. MMD has experienced a significant impact on its safety culture by delivering targeted content, promoting transparency and sharing of knowledge to drive continuous improvement. “Using the Axonify platform was thinking outside of the box for MMD. It was a different way to engage our employees,” says Grofic. “There’s a great energy around the entire program, and each site is taking the initiative to come up with unique ideas around how they can continue to drive this energy around SbC and safety overall.”