4 ways to prioritize warehouse productivity with distribution and logistics workers
Everything from the products and services you deliver to the processes and technologies you use to create them is evolving. That can mean organizations can find operational efficiencies they never thought possible. But it can also lead to disruptions that cause a ripple effect across the enterprise—right down to the distribution floor. When your distribution and logistics workers lose pace with the rate of change, knowledge and skills gaps grow and that impedes warehouse productivity and safety—and hurts your bottom line.
But here’s the good news: there are ways to enable your staff to stay on track, delivering the productivity and quality your organization needs. Here are four ways to prioritize productivity with distribution and logistics workers.
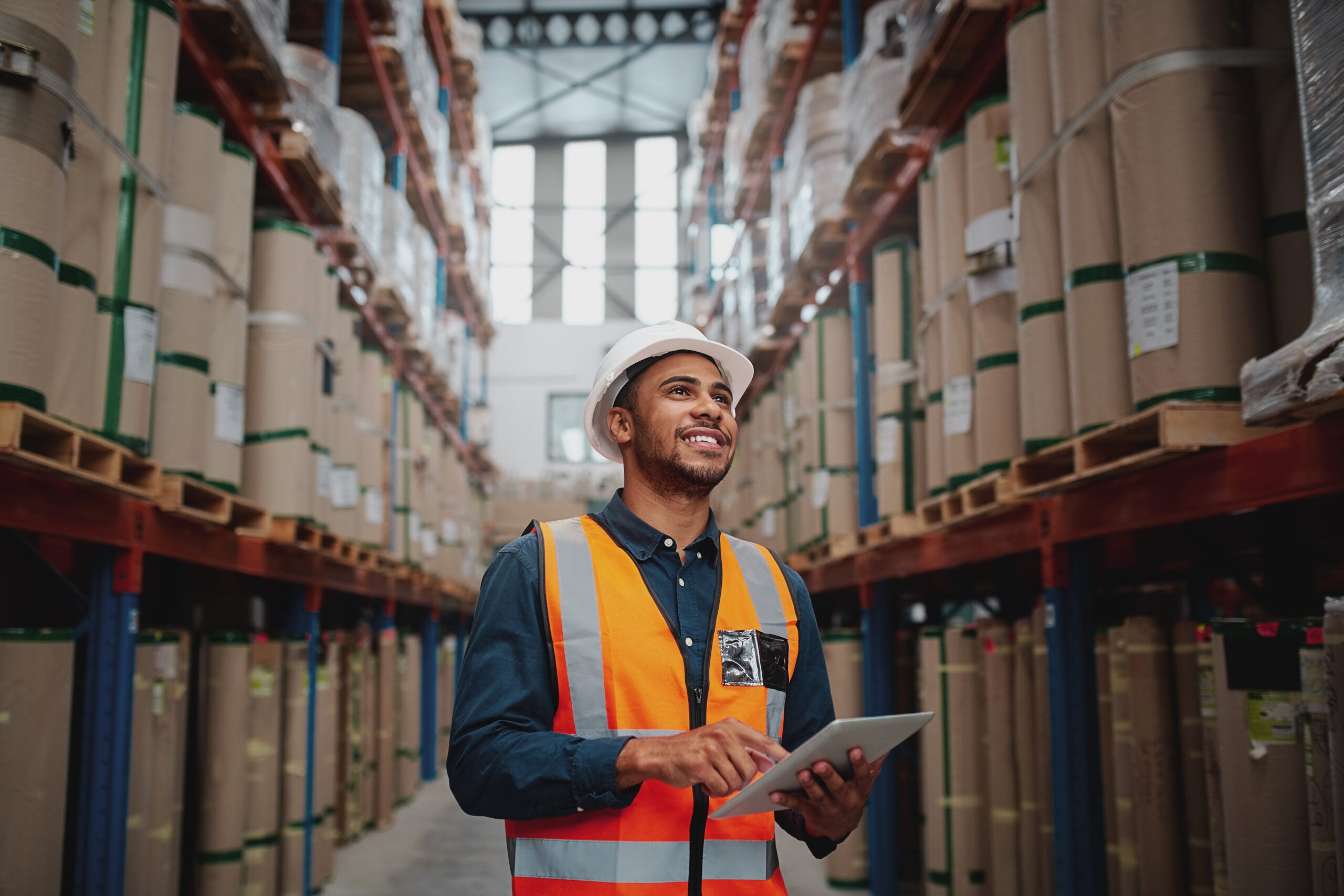
1. Make learning a daily habit
Productivity starts with consistent and correct adherence to procedures—and to achieve that consistency, your staff needs the right training. But we’ve said it before: people are programmed to forget. To keep processes and protocols top-of-mind, your staff need regular and ongoing training and reinforcement to embed and establish the learnings deep in their memory. Does this mean you need to strain on the floor and production managers to do daily refresher training? Nope—you just need the right technology in place to serve up short bursts of training every day, on the devices they’re already using, that personalizes learning paths to ensure that every worker knows what they need to know, in the moment they need to know it. That’s the foundation of productivity.
2. Build safety into your culture
Minimizing risk and injuries—and line disruptions—is crucial to prioritizing warehouse productivity. But rather than relying on annual compliance courses that are just as disruptive—and easily forgotten—bake safety and compliance into the culture of your organization. What does that look like? It means regular (ideally daily!) safety training that keeps crucial information top-of-mind. It means identifying and addressing knowledge gaps before they become a hazard. And it means reinforcing this safety culture through daily huddles, internal communications, recognition, rewards and more. In short: making safety a daily conversation, not an annual one.
3. Keep an eye on skills and knowledge gaps, not just mistakes
You might be able to track knowledge gaps at the distribution floor level, but that’s a reactive approach—you won’t know you have a problem until the mistake has already happened. Rather than track mistakes, proactively monitor skills and knowledge gaps. That way you can see potential risks before they impact productivity—and, better yet, identify opportunities to improve processes with additional training or employee development. It might seem like a daunting task to identify and address knowledge gaps at scale. After all, if you have 150,000 workers, how can you monitor all the risks that could derail productivity? But with the right technology and knowledge gap strategies in place, these gaps can be easily flagged and addressed—before an incident occurs.
4. Create a consistent and clear line of communication
The ROI of frontline communication cannot be overstated. Providing your distribution and logistics staff with effective channels of communication and feedback creates a direct connection between your frontline and your head office. A critical need, considering our recent research found that only 39% of frontline workers feel heard. Creating a strong line of communication also creates opportunities for idea-sharing, community building and much more.
—
Productivity and warehouse efficiency is top-of-mind for every distribution and logistics organization. And by investing in the right enablement and support for staff, organizations can quickly and easily remove many of the disruptors that are impacting the ability to get things done.