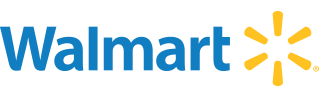
Walmart achieves unprecedented safety results by building employee knowledge and translating it into job action
When you’re in charge of one of the largest distribution networks and private trucking fleets in the world, how do you create a safety culture that will positively and dramatically decrease risk, reduce accidents and injuries along with associated costs, as well as improve employee engagement?
“These were the questions facing Ken Woodlin in 2010 when he was appointed Vice President of Compliance, Safety and Asset Protection for Walmart Logistics.
“When I came into this role, I was fortunate to inherit a safety program with compliance components, such as policies and procedures, already in place,” said Woodlin. “But we wanted to build a world-class safety culture, which meant we had to deal with several challenges.”
Identifying key challenges
Safety incidents across the Walmart organization have a significant cost. Woodlin knew if he could achieve a 5% reduction in Occupational Safety and Health Administration (OSHA) recordables, this could save Walmart millions each year. But to improve safety, Woodlin also knew he needed a way to generate more employee awareness around safety policies and procedures, keep this top of mind, and ensure employees could translate this knowledge into safe practices on the job.
“We knew a big part of changing behaviors and beliefs about safety would involve building employee knowledge. And we knew we’d need an innovative approach to do that,” said Woodlin. “In our workforce, we have four distinct generations—Traditionalists, Baby Boomers, Generation X, and Millennials—each with their own learning preferences. We also have distribution centers all over North America, each with their own safety cultures, but they also needed to be on board with the overall corporate safety culture. In short, we needed a solution that could be tailored to meet the needs of our different groups of learners.”
Besides appealing to a multi-generational workforce, Woodlin was also looking for a solution that would meet several key requirements:
- Engage associates ongoing
- Reinforce safe work practices continually
- Ensure fast and easy access to training to avoid time away from work
- Provide personalized learning so that each employee could progress at his/her own speed and build on their individual baseline knowledge
- Allow the company to identify and predict at-risk behaviors so they could address them proactively
Implementing a revolutionary approach for building employee knowledge and changing behavior
In 2012, Woodlin began implementing the Axonify solution. In a nutshell, Axonify helps employees build, sustain, and share knowledge in a fun, engaging, and gamified way. It personalizes learning to target and close individual knowledge gaps, giving employees the confidence to perform their roles to the best of their ability. And this helps organizations achieve their potential because employees have the right knowledge in their heads and at their fingertips, which ultimately drives real business results.
Today, more than 75,000 Walmart associates in more than 150 distribution centers across the United States engage with the Axonify solution. During each shift, these associates log on to the Axonify platform (while they have some down time) and spend 3-5 minutes playing a fun game while answering safety questions. Since Axonify provides instant feedback, employees know which questions they’ve answered correctly and where they need improvement. Since the system also remembers their responses, the next time employees log in, they receive questions to reinforce information they know, as well as follow up on information they don’t know. This ensures knowledge increases and associates don’t forget what they’ve learned previously. Besides this, employees can see their individual progress as well as how they measure up against their peers, sparking friendly competition between coworkers.
Once employees begin receiving learning through Axonify, Walmart uses the Axonify Behaviors module to determine if they are actually applying the information they learn on the job. The company defines optimal performance behaviors and then observes employees on the job to determine if they are following safety procedures correctly or incorrectly. Once Walmart imports the behavior observations into Axonify, the system automatically evaluates them and immediately adjusts the training and reinforcement employees receive. This ensures employees get the learning they need to help them take the right actions at work.
Through this process, Walmart can now identify areas where safety behaviors are not being performed correctly and proactively investigate and address these issues before they become a bigger problem. For example, if the company determines employees are not meeting ladder safety standards, they can look at if the learning content itself is insufficient or if there is another reason why employees are not following ladder safety procedures correctly to mitigate employee injuries. Axonify can even help Walmart predict at-risk behaviors based on the data collected in the system to proactively address those behaviors before safety incidents occur.
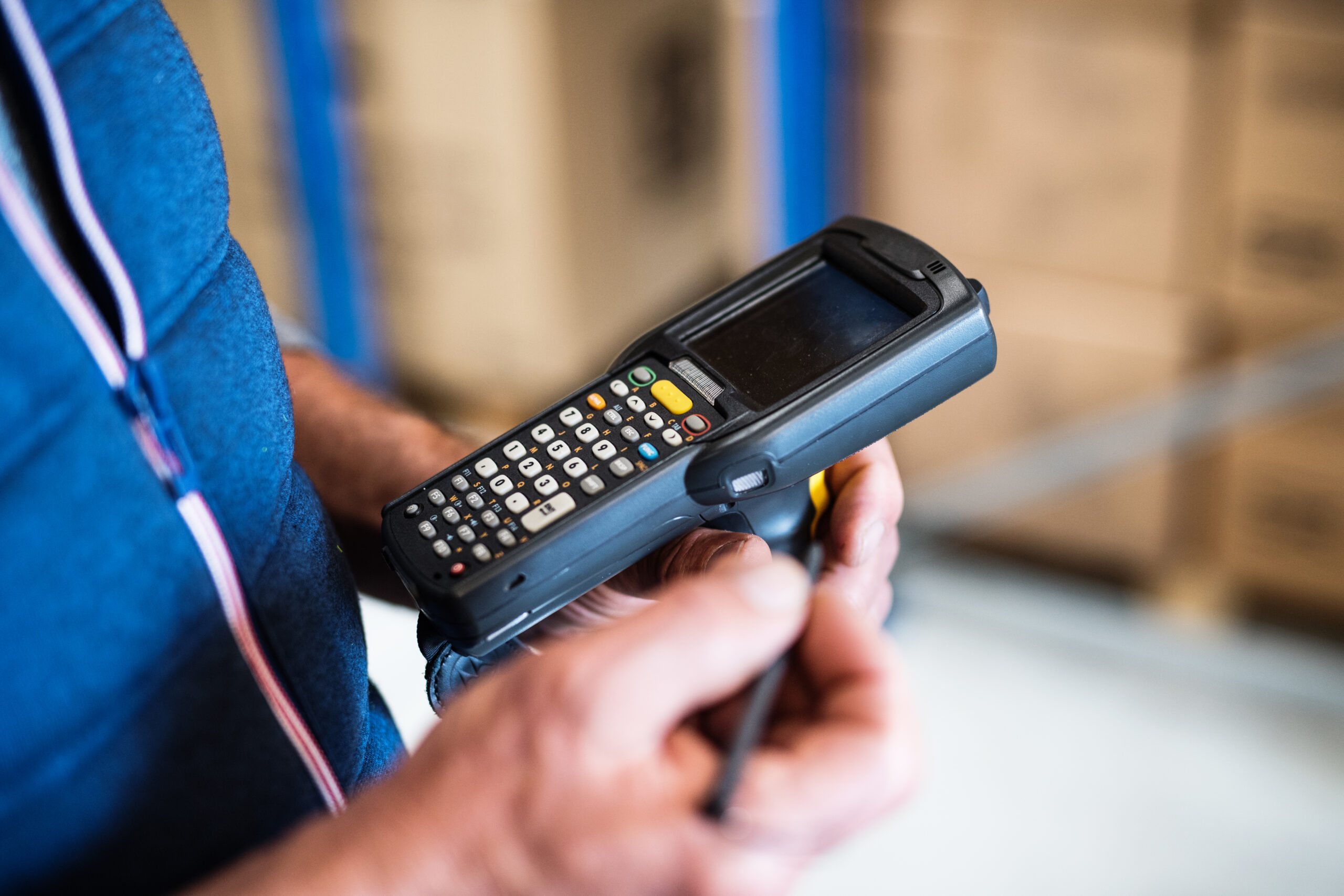
Tying learning to business results
Fast-forward to today and Walmart’s existing safety program, which was already solid, is now arguably the world’s best:
- Recordable incidents at 8 of Walmart’s distribution centers decreased by 54% during the pilot, morale has been elevated, and injury expenses mitigated
- 96% of behavior observations have been positive, meaning employees are applying their knowledge on the job
- Voluntary participation on the Axonify platform averages 91%
- Knowledge levels on topics around safety have increased as much as by 15%
- Employee confidence in the material has increased by as much as 8%
“We have seen tremendous improvement as a result of our associates’ ownership and engagement in our safety programs, as well as leadership commitment to the program,” says Woodlin. “Metrics like Lost Times have been reduced by more than 50% and Incident Rates and DART rates [days away from work, job restrictions, and/or job transfers] are well below industry average. Feedback about the Axonify platform has been phenomenal, and we believe the process has been a significant contributing factor to our improved performance and engaged associate base.”
Since Walmart implemented Axonify more than four years ago, associates have become more able to spot potential safety opportunities, see the connectivity of safety in the workplace with safety out of the workplace, and have also become more comfortable raising safety concerns. One of the best parts, according to Woodlin, is that safety training has become a “continuous loop,” driven by good behaviors and fed by the corporate culture, rather than a one-way, top-down approach.